Login to your Account
Password Reminder
Password Reminder
Password Reminder
SNACK MANUFACTURING PROCESS
Click on any circle to view the process step manufacturing
PACKING
Primary Packing
The flavoured chips / crisps are fed from a conveyor belt onto the multi-head weigher sitting above the packaging machine. Here the 8 - 14 head weighers select the 'best' combination of heads to give the packet weight desired. Running at speeds up to 150 packs per minute this is a process which requires accuracy and speed and the discharge of product to the packaging machine in 'discrete' portions (i.e. all at once and not strung out). The packets are formed from a reel of packaging film. The chips / crisps drop into the open packet chute, which is then sealed top and bottom by heated jaws, and cut to length by a knife.As the chips fall into the packet a metal detector checks for the presence of any foreign bodies and rejects the pack if the check is positive.
Sealed packets are checked to ensure that they are sealed correctly and that their weight complies with all relevant legislation. Sufficient air is incorporated within the sealed packs to help guard against breakages. A further metal detection inspection may also be carried out on the packets before multi-packing or cartoning.
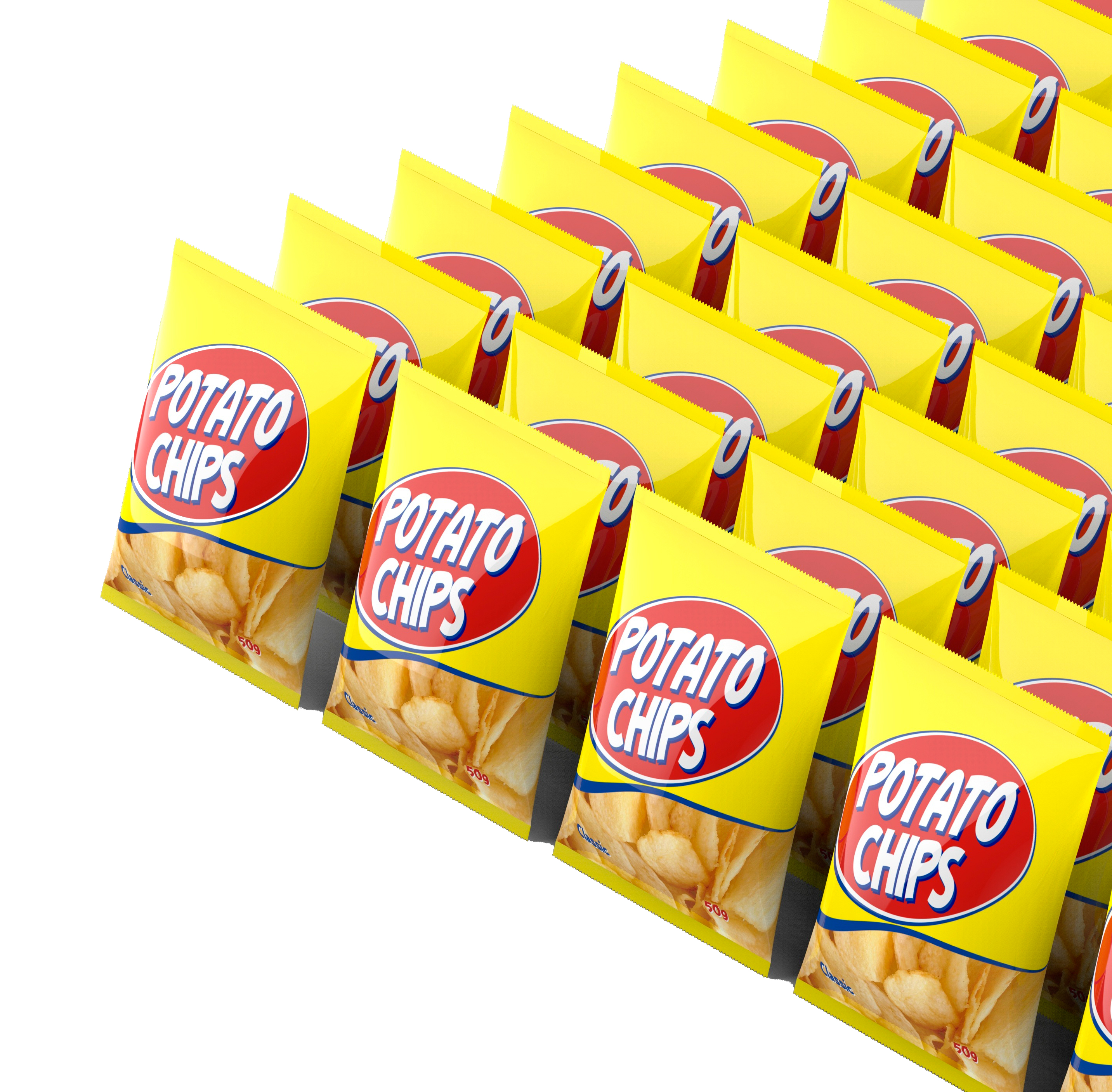
Date stamping
Every packet of chips / crisps is stamped with a special code. Using this code, the manufacturer can trace when the products were made and even on which packaging machine. This information can be used to identify which raw materials were used to make the product with full traceability along the whole supply chain being possible. This can be useful if there is a problem with the product. A 'best before' date is also stamped on the packet. For the product to be at its best, the chips / crisps should be eaten by this date. Their quality cannot be guaranteed after this..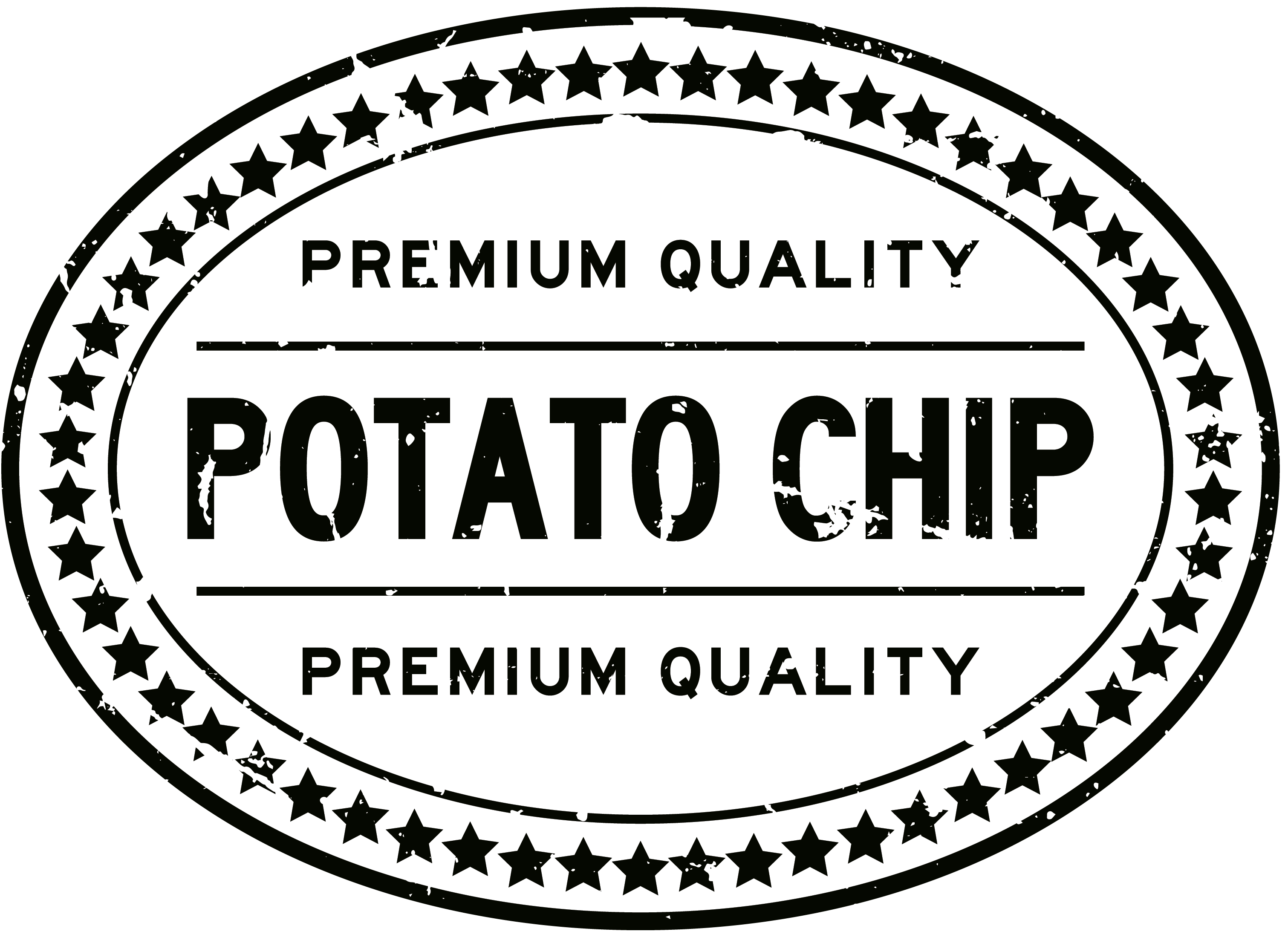
Secondary Packing
The individual packets of chips / crisps are either made into multi-packs or packed into cardboard boxes or trays for transit. Multi-packing involves collating the individual packets in 6s, 12s, 16s, 24s, etc., and wrapping them in a multipack outer for sale in that format. Traditionally this operation would have been carried out manually or semi-automatically but is nowadays mostly fully automated. Not only can multiples of the same individual packets be made into multi-packs but also an infinite range of flavours and/or products as the process allows. This offers a vast choice for consumers and great value.The multi-packs or individual packs are then placed into cartons either manually or using automatic case-packers. The boxes are then stamped with the 'best before' date so that the shop keeper can identify the age of his stock and ensure it is rotated properly. This 'secondary packaging' protects the chips during transport.
Packed and sealed cases are then given a final metal detection inspection before being stacked on to pallets either manually or using automatic palletising equipment. The stacked pallet is typically then stretch-wrapped to improve the stability of the palletised load. The finished pallet is then moved from the production area to the distribution department and onwards to supermarkets and local shops.
That is the end of the process. The chips / crisps are then transported to the shops. Then millions of us buy and enjoy them every day.
You also may be interested in ...
Savoury Snack Market
Read about the snack industry we represent.
Product Diversity
Discover the diversity of snacks.